Executive Vice President
Olivier Leclercq was born and raised in Roubaix, France. He volunteered and enrolled with the French Paratrooper’s on his 17th birthday and later served as the youngest ever non-commissioned officer of a RPIMA Paratrooper French Marine’s Regiment. After the military, he joined Decathlon, which was founded by his father in 1976. During his time there, Olivier proved himself as an accomplished businessman and entrepreneur. In 1986 He initiated the production of numerous products and spent 12 years based in various Asian countries. Following that, he progressed with the company as a Board Member, Audit Committee President, Chairman of the Investment Strategic Committees, and ultimately served as the Group President. By the time Olivier left in 2012, he had grown Decathlon into the largest sporting good production and retail organization in the world, employing over 55,000 people in 20 countries with over a dozen specific brands.
He is succeeded at Decathlon by his younger brother Matthieu and has since then served as a Managing General Partner and Vice President of the Strategic Committee for the Mulliez family holdings which employs more than 520,000 people in various industries throughout 30+ countries. Mr. Leclercq joined ACI Jet as an investor and Executive Vice President in 2014. With his extensive background in the retail industry, he brings a deep knowledge of and passion for marketing and the customer experience to the company.
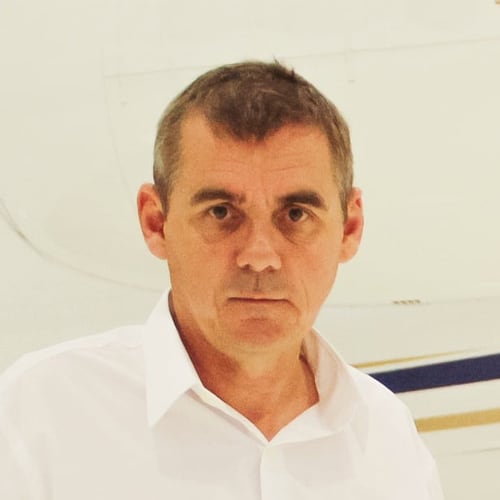