"What Lies Beneath..."
Cessna Citation 550 Gets New Wing Skin (2018)
- Aircraft: Cessna Citation 550
- Date: January, 2018
- Key Contributor(s): Repair Station Sheet Metal Experts
The aircraft was an early 1990’s model Citation 550 that was visiting ACI Jet MRO for a Phase 1-4 inspection. During the inspection, after peeling back the de-icing boot, it became apparent that something was wrong. The boot had been installed incorrectly during a previous maintenance visit at another facility. As a result, corrosion began to appear on the wing skin which, for those who don’t know, is the fuel tank itself.
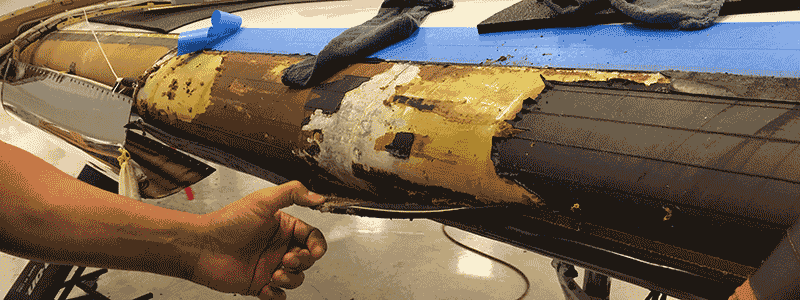
The most challenging part would be fitting the new wing skin on the aircraft, not just the work of installing it. Drilling holes in very specific locations on a massive curved surface in order for the skin to mount without any gap whatsoever and allow it to function as a fuel reservoir is no easy task. Any error, on just one of the nearly 1,000 holes, would “cost the company royally,” as the project lead put it.
As they say, “the best laid plans of mice and men.” When the skin arrived from Textron, there were two stiffeners bonded onto the skin for strength, but which made fitting and installation physically impossible. Again, this had never been done before. We did have a team with unrivaled experience when it comes to sheet metal work. A Lockheed veteran on the team knew that “I can’t do it” was never an option as a response to a challenge. The same guy who built SR-71s for Skunkworks and held seven specified classifications was now on the task. A solution was devised that was approved by independent design engineers in which portions of the stiffeners would be cut and removed, then re-spliced back on for installation.
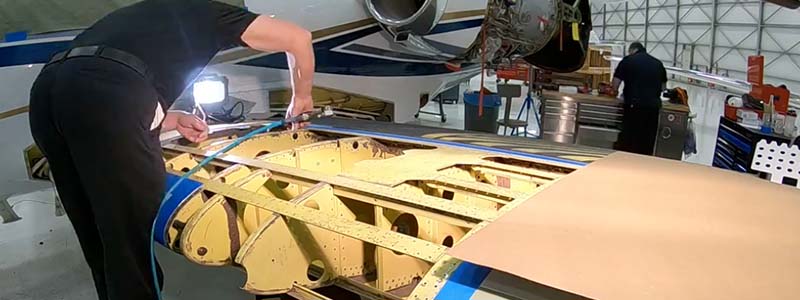
Then came the meticulous and arduous task of locating, drilling, re-locating, drilling a bit more, finding someone small enough to climb halfway into the wing, sealing and securing. Cap the project off with a small paint booth visit and voila: no leaks, no asymmetry (you’re welcome, readers with OCD) and no visible difference from before, which is both satisfying and a bit annoying after so much work.
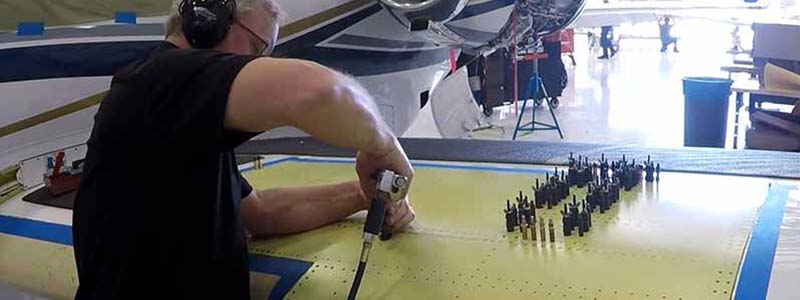